Diana4D is a powerful software used for structural analysis and design, particularly for advanced finite element modeling in engineering. Whether you’re an experienced structural engineer or a beginner, leveraging Diana4D to its full potential requires understanding best practices for effective and efficient modeling diana4d. This guide will walk you through the most essential strategies to master the modeling process in Diana4D.
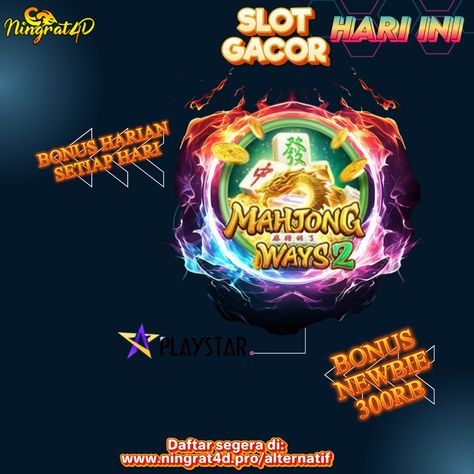
1. Understand the Basic Modeling Workflow
Before diving into the details, it’s essential to have a clear understanding of Diana4D’s modeling workflow. The process typically involves the following steps:
- Geometry Modeling: Define the structural elements of your project.
- Mesh Generation: Discretize the geometry into finite elements for numerical analysis.
- Material and Section Assignment: Assign properties like material types, thickness, and cross-sectional areas to the elements.
- Boundary Conditions and Loads: Apply supports, constraints, and loads to simulate real-world conditions.
- Analysis Setup and Solution: Select analysis types and solve the model.
Starting with a clear understanding of each step allows you to ensure that the entire modeling process is systematic and aligned with best practices.
2. Model with a Clear Purpose
When building a model, always start with a well-defined purpose. Consider the objective of your analysis, whether it’s static, dynamic, or something else. Understanding the physical phenomenon you’re trying to simulate—such as stresses, displacements, or thermal effects—will help you decide which elements to include and how to best represent them.
Key points to consider:
- Simplify when possible: If the phenomenon you are simulating doesn’t require complex features, use simplified models. For example, you might not need to model every minute detail like small holes or cracks if they won’t affect your results significantly.
- Accuracy vs. Efficiency: Strive for a balance between model complexity and the accuracy of the results. More elements and finer meshes will lead to more accurate results but may also increase computation time.
3. Use Appropriate Element Types
Diana4D offers a variety of element types, each suited for specific tasks. Choosing the right element type for each part of the structure is crucial to ensure efficiency and accuracy.
- Beam Elements: Used for modeling linear, one-dimensional structures like beams and columns.
- Shell Elements: Suitable for thin-walled structures such as slabs or walls.
- Solid Elements: Best for modeling three-dimensional solid structures with complex geometry.
Select elements that best represent the actual structure while keeping computational efficiency in mind. Overusing solid elements, for instance, might lead to unnecessarily high computation time when simpler beam or shell elements can provide sufficient accuracy.
4. Create a Quality Mesh
Mesh generation is a critical step in finite element modeling. A poorly structured mesh can lead to inaccurate results or long computational times. Here are some key considerations for generating a high-quality mesh:
- Element Size: In general, smaller elements provide more accurate results but at the cost of higher computational demand. Use finer meshes in areas with high gradients or where you expect large stress concentrations.
- Refining Meshes: For complex geometries or critical areas (like joints or supports), refining the mesh around these regions helps capture the details better.
- Mesh Regularity: Strive for a regular, uniform mesh in regions that don’t have high stress gradients. Irregular or skewed elements can lead to errors or unstable solutions.
5. Material Properties and Section Assignments
Accurate material modeling is key to ensuring the reliability of your results. Diana4D supports a variety of materials, including isotropic, orthotropic, and non-linear materials. Here’s how you can get the most out of it:
- Accurate Material Data: Ensure that the material properties (like Young’s modulus, Poisson’s ratio, yield strength, etc.) are based on real-world data or verified sources.
- Non-linear Behavior: If the material exhibits non-linear behavior, such as plasticity or creep, make sure to apply appropriate models that capture these effects accurately.
- Check Units Consistency: Diana4D uses consistent units throughout the software, but always double-check that your material properties are input correctly to avoid calculation errors.
6. Assign Boundary Conditions and Loads Carefully
Boundary conditions and loads simulate how a structure will behave under real-world constraints. Applying the wrong boundary conditions can lead to unrealistic results. Here’s how to do it effectively:
- Boundary Conditions: Accurately model the supports and constraints of your structure. For instance, fixed supports should be used where the structure is rigidly held, while roller supports should allow movement in certain directions.
- Load Application: Ensure that loads are applied correctly, both in terms of magnitude and direction. Diana4D allows you to apply point loads, distributed loads, and temperature effects, so be sure to choose the most appropriate type for your analysis.
- Check for Compatibility: Make sure that the boundary conditions and loads are compatible with the physical behavior you’re simulating. For example, ensure that you don’t accidentally apply a fixed boundary condition in an area where the structure can move.
7. Perform Sensitivity Analysis
Before finalizing your model, it’s important to conduct sensitivity analyses to ensure that your results are reliable and not overly dependent on certain assumptions. Small changes in input values (like material properties or boundary conditions) should not result in large discrepancies in your analysis results. Sensitivity analysis helps you identify the critical parameters that most affect the outcome and verify your model’s robustness.
8. Post-Processing Results for Insightful Analysis
Once your model has been analyzed, the next step is post-processing the results. Diana4D provides various tools for visualizing and interpreting the results, such as:
- Deformed Shape Visualization: View how the structure deforms under the applied loads.
- Stress and Strain Contours: Display the distribution of stress and strain across the structure to identify potential failure points.
- Displacement Analysis: Identify any areas with excessive displacements that may need design modifications.
By interpreting your results effectively, you can ensure that your design is safe, efficient, and cost-effective.
9. Documentation and Model Review
Finally, documentation is crucial. Keep track of every step you take in your modeling process for future reference. This includes:
- Model Descriptions: Clearly describe the geometry, loads, boundary conditions, and material properties.
- Assumptions: Document any assumptions you made during the modeling process to clarify the context for future analyses.
- Version Control: Maintain version control to track changes and ensure that you can refer back to previous iterations.
A thorough review of your model by a colleague or supervisor can help spot any mistakes or missed opportunities for optimization.
Conclusion
Modeling in Diana4D requires a mix of technical understanding and careful attention to detail. By following these best practices—planning your model, choosing the right elements, creating a high-quality mesh, applying correct boundary conditions, and interpreting results carefully—you’ll be well on your way to mastering Diana4D and using it to solve complex structural analysis problems effectively.